5 Whys Root Cause Analysis
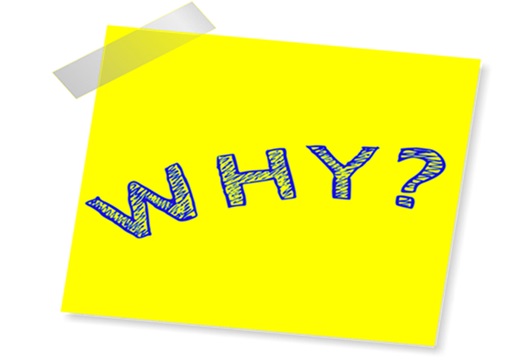
The 5 Whys Analysis is a simple yet effective technique used to explore the root cause of a problem by repeatedly asking the question “Why?” five times, or as many times as necessary, to reach the underlying issue. Developed by Sakichi Toyoda, a Japanese industrialist and inventor, the 5 Whys technique was popularized within Toyota as part of its Toyota Production System (TPS) in the 1950s. It has since become widely used in various industries, including manufacturing, healthcare, IT, and business, as a valuable tool for root cause analysis (RCA).
In today’s fast-paced business and industrial environments, identifying and addressing the root causes of problems is critical for minimizing downtime, improving efficiency, and ensuring long-term success. By focusing on the root cause rather than the symptoms, organizations can prevent problems from recurring and implement effective corrective actions.
This comprehensive guide will explore:
- What is 5 Whys Analysis?
- Why is 5 Whys Important?
- How to Implement 5 Whys Analysis
- Applications in Various Industries
- Manufacturing
- Healthcare
- IT and Software Development
- Business and Process Improvement
- Common Pitfalls and Challenges
- Case Studies
- Best Practices and Tips for Effective 5 Whys Analysis
1. What is 5 Whys Analysis?
The 5 Whys Analysis is a problem-solving technique that involves asking “Why?” five times to drill down into the cause-and-effect relationship of a problem. The goal is to identify the root cause of an issue by tracing back through the series of causes leading to the problem.
Here’s an example:
Problem: A car won’t start.
- Why? – The battery is dead.
- Why? – The alternator is not functioning.
- Why? – The alternator belt is broken.
- Why? – The alternator belt has not been replaced.
- Why? – The car’s maintenance schedule was not followed.
In this example, the root cause of the problem is a failure to follow the maintenance schedule, which led to the alternator belt breaking and the battery dying. By identifying this root cause, the organization can take corrective action, such as improving the maintenance schedule, to prevent the problem from recurring.
Key Principles of the 5 Whys Technique:
- Simplicity: The method is easy to understand and can be quickly applied without requiring complex tools.
- Iterative Process: Although five iterations are common, the actual number of "Whys" may vary depending on the complexity of the problem.
- Focus on Process, Not People: The analysis focuses on problems within the process, not on blaming individuals.
- Preventive Approach: By identifying and addressing the root cause, the technique helps to implement long-term solutions rather than temporary fixes.
2. Why is 5 Whys Important?
The 5 Whys Analysis offers several advantages for problem-solving and root cause identification, making it a critical tool in quality control and continuous improvement efforts.
A. Simplicity and Accessibility
One of the most significant benefits of the 5 Whys method is its simplicity. No specialized training or advanced tools are required, making it accessible to teams at all levels of an organization. It encourages immediate engagement and critical thinking, making it a versatile tool for quick problem-solving.
B. Identifying Root Causes
While many problem-solving approaches focus on addressing surface-level symptoms, the 5 Whys Analysis digs deeper into the issue to uncover the root cause. Understanding the root cause enables organizations to prevent recurrence and avoid wasting resources on superficial fixes.
C. Collaboration and Cross-Functional Input
The technique encourages input from different departments and team members, promoting collaboration and a holistic approach to problem-solving. This helps eliminate bias and ensures that all potential causes are considered during the analysis.
D. Continuous Improvement
By using 5 Whys as part of a continuous improvement cycle, organizations can systematically eliminate inefficiencies, defects, and quality issues over time. It is commonly used in lean manufacturing and Six Sigma methodologies to promote a culture of continuous process improvement.
3. How to Implement 5 Whys Analysis
Implementing the 5 Whys Analysis requires a structured approach to ensure that the root cause is properly identified. Below is a step-by-step guide to conducting a successful 5 Whys analysis:
Step 1: Define the Problem
The first and most crucial step is clearly defining the problem. Ensure that everyone involved agrees on the problem statement. The problem should be specific and measurable to avoid vague or ambiguous answers.
Example: A product fails quality testing.
Step 2: Assemble a Team
Bring together a cross-functional team of individuals familiar with the process or issue. Including diverse perspectives ensures that all possible causes are considered, and the analysis is not limited to one point of view.
Step 3: Ask the First “Why?”
Ask the first “Why?” to determine why the problem occurred. It’s essential to base the response on actual data and facts rather than assumptions.
Example: Why did the product fail quality testing?
- The material used did not meet specifications.
Step 4: Continue Asking “Why?”
For each answer, continue asking “Why?” until the root cause is identified. This typically involves five iterations, but more may be needed in complex cases.
Example:
- Why did the material not meet specifications?
- The supplier delivered incorrect materials.
- Why did the supplier deliver incorrect materials?
- The purchase order was incorrect.
- Why was the purchase order incorrect?
- The specifications were not properly communicated.
- Why were the specifications not communicated?
- The employee in charge of the purchase order was not trained properly.
Step 5: Identify the Root Cause
Once you’ve asked “Why?” enough times, you will arrive at the root cause of the problem. The root cause in this example is the lack of training, which led to incorrect purchase orders and poor material quality.
Step 6: Implement Corrective Actions
After identifying the root cause, the next step is implementing corrective actions. The solution should address the root cause and prevent the problem from recurring.
Step 7: Monitor Results and Adjust
Monitor the implementation of corrective actions and verify their effectiveness. If the problem persists, revisit the analysis and continue asking “Why?” to ensure no underlying causes were missed.
4. Applications in Various Industries
The 5 Whys Analysis is used across many sectors, offering versatile problem-solving capabilities. Some of the key industries where 5 Whys is applied include:
A. Manufacturing
In manufacturing, the 5 Whys method is widely used to improve quality control, identify process inefficiencies, and reduce downtime. When defects or equipment failures occur, 5 Whys can help manufacturing teams uncover process-related causes, such as equipment malfunctions, operator errors, or supply chain issues.
Example: A packaging line stops functioning.
- Why did the packaging line stop?
- The machine overheated.
- Why did the machine overheat?
- The cooling system failed.
- Why did the cooling system fail?
- Maintenance was not performed on schedule.
- Why was maintenance not performed?
- There was no maintenance schedule in place.
The root cause here is the absence of a maintenance schedule, and corrective action would involve establishing regular maintenance protocols.
B. Healthcare
In healthcare, 5 Whys is often applied to patient safety issues, clinical processes, and healthcare-associated infections (HAIs). By drilling down into the causes of adverse events or errors, healthcare providers can implement systems to reduce risks and improve patient outcomes.
Example: A patient received the wrong medication.
- Why did the patient receive the wrong medication?
- The nurse administered the wrong drug.
- Why did the nurse administer the wrong drug?
- The medication label was unclear.
- Why was the medication label unclear?
- There was a miscommunication between the pharmacy and nursing staff.
- Why was there a miscommunication?
- There was no standardized handoff procedure between the pharmacy and nurses.
The root cause here is the lack of a standardized communication process, which could be resolved by introducing formalized handoffs.
C. IT and Software Development
In IT, 5 Whys is employed to troubleshoot system failures, software bugs, and cybersecurity breaches. The fast-paced nature of software development means that issues often arise from communication breakdowns, missed deadlines, or flawed coding practices.
Example: A website crashed during a high-traffic period.
- Why did the website crash?
- The server could not handle the load.
- Why couldn’t the server handle the load?
- The server was not upgraded for expected traffic.
- Why wasn’t the server upgraded?
- The IT team didn’t anticipate the traffic surge.
- Why didn’t the IT team anticipate the surge?
- There was no traffic forecasting model in place.
The root cause was the absence of traffic forecasting, so corrective action would be implementing a system to anticipate traffic spikes.
D. Business and Process Improvement
In business operations, 5 Whys can help organizations address inefficiencies, reduce waste, and improve customer satisfaction. It’s a fundamental tool in lean manufacturing, Six Sigma, and total quality management (TQM).
Example: Customer complaints about delayed orders.
- Why are orders delayed?
- The shipping department is overwhelmed.
- Why is the shipping department overwhelmed?
- There is a backlog of orders.
- Why is there a backlog of orders?
- Production is behind schedule.
- Why is production behind schedule?
- There was a supply chain delay.
- Why was there a supply chain delay?
- The supplier did not deliver materials on time.
The root cause is the supplier delay, and corrective actions could involve renegotiating supplier contracts or finding secondary suppliers.
5. Common Pitfalls and Challenges
While the 5 Whys method is simple, there are several common challenges and pitfalls that teams should be aware of when conducting the analysis:
A. Superficial Answers
One of the most common pitfalls is stopping the analysis too early and not reaching the true root cause. Teams may be satisfied with the first or second "Why?" when a deeper issue remains.
B. Focusing on Symptoms, Not Causes
Teams often confuse symptoms with root causes, leading to solutions that address only the surface issues without solving the underlying problem. For example, addressing equipment failure without analyzing why the failure occurred in the first place will not prevent future occurrences.
C. Bias in Analysis
Another challenge is bias or preconceived notions. Participants may assume they know the answer before conducting the analysis, leading to incomplete or skewed results. Cross-functional collaboration helps mitigate this by bringing in diverse perspectives.
D. Over-Complicating the Process
The simplicity of the 5 Whys is one of its strengths. However, over-complicating the process by adding unnecessary steps or overthinking the answers can dilute the effectiveness of the analysis.
6. Case Studies
Case Study 1: Automotive Industry
In the automotive industry, Toyota famously applied 5 Whys to reduce manufacturing defects. After discovering frequent engine malfunctions, the team used the 5 Whys to trace the issue to incorrect part assembly. The root cause was identified as a missing training protocol for assembly workers, and Toyota implemented corrective actions by improving worker training and standard operating procedures.
Case Study 2: IT Sector
A tech company experienced frequent downtime due to server crashes. After using the 5 Whys method, they discovered that their server infrastructure was outdated and lacked proper load balancing. The root cause was traced to a lack of budget approval for system upgrades. The company restructured its IT budget process, allowing for regular system updates and preventing future crashes.
7. Best Practices and Tips for Effective 5 Whys Analysis
To get the most out of 5 Whys Analysis, consider the following best practices:
- Involve Cross-Functional Teams: Include members from different departments to get a broader perspective on the problem and its potential causes.
- Base Answers on Facts: Ensure that the answers to each "Why?" are based on actual data and observations, not assumptions or guesses.
- Avoid Blame: Focus on the process rather than individuals. The goal is to improve the system, not to assign blame.
- Document the Process: Keep a record of the 5 Whys analysis for future reference and to help with continuous improvement efforts.
- Review Regularly: Conduct periodic reviews of the 5 Whys analysis to ensure that corrective actions have been implemented effectively.
Conclusion
The 5 Whys Analysis is a powerful and versatile tool for identifying root causes and implementing long-term solutions. Its simplicity makes it accessible to all levels of an organization, while its structured approach promotes thorough investigation and problem-solving. By applying the 5 Whys across various industries, from manufacturing to healthcare and IT, organizations can address inefficiencies, improve processes, and foster a culture of continuous improvement. When combined with other quality control tools and methodologies, the 5 Whys technique helps build more resilient and efficient systems.