Total Quality Management
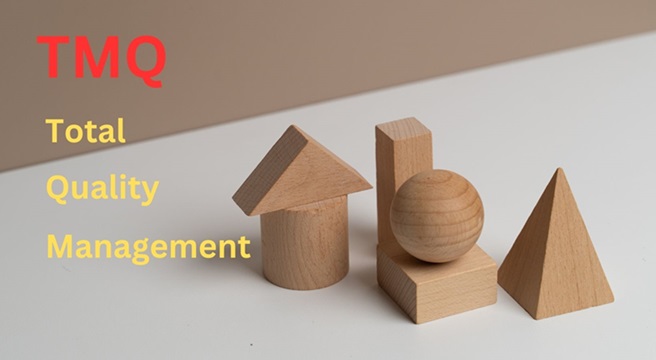
In the contemporary business environment, ensuring consistent quality is no longer just a competitive advantage; it’s a necessity for survival. One of the most influential management philosophies developed to improve organizational quality and customer satisfaction is Total Quality Management (TQM). Originating in the mid-20th century, TQM has since become a global standard for organizations striving to enhance product and service quality across all functions.
This guide explores the history, principles, tools, benefits, challenges, and best practices associated with Total Quality Management.
What is Total Quality Management (TQM)?
Total Quality Management (TQM) is an organizational approach aimed at improving quality and performance to meet or exceed customer expectations. It involves the continuous improvement of processes, products, services, and organizational culture. Unlike traditional quality control, which focuses on identifying defects post-production, TQM is preventive and comprehensive, involving all employees at all levels and integrating quality considerations into every part of the organization.
TQM is based on the idea that quality is not the responsibility of a single department but is a collective effort by the entire organization. This approach requires cultural change, employee involvement, leadership commitment, and continuous improvement to drive long-term success.
History and Evolution of TQM
The concept of TQM evolved from earlier quality control methodologies, notably the work of quality pioneers such as W. Edwards Deming, Joseph Juran, and Philip Crosby. The principles of TQM developed over time, building upon statistical process control, quality assurance, and continuous improvement.
- W. Edwards Deming: Considered the father of modern quality management, Deming introduced the idea that quality should be integrated into all organizational processes. He is well-known for the Deming Cycle (Plan-Do-Check-Act) and the concept of 14 Points for Management, which promote continuous improvement and focus on systemic quality issues.
- Joseph Juran: Juran’s Quality Trilogy (quality planning, quality control, and quality improvement) emphasized the importance of leadership in driving quality improvement initiatives. He introduced the concept of "fitness for use," which emphasizes meeting customer needs.
- Philip Crosby: Known for popularizing the phrase “quality is free,” Crosby advocated that the cost of poor quality far outweighs the investment in quality improvement. He emphasized the importance of zero defects and coined the idea that “quality is conformance to requirements.”
The principles of TQM were further developed and formalized during the quality movement in Japan in the 1950s and 1960s, where organizations such as Toyota integrated continuous improvement practices into their manufacturing processes. TQM gained global recognition and was widely adopted across industries during the 1980s and 1990s.
Core Principles of Total Quality Management
TQM is built on a set of guiding principles that shape its implementation and success. These principles can vary slightly depending on the organization and industry, but some core ideas are universally accepted.
- Customer FocusThe primary goal of TQM is to meet or exceed customer expectations. Every action taken in an organization, from process design to service delivery, must aim to enhance customer satisfaction. In TQM, both external and internal customers (employees and departments) are equally important.
- Continuous Improvement (Kaizen)TQM promotes an ongoing effort to improve products, services, and processes. This philosophy, known as Kaizen in Japanese, emphasizes incremental changes that lead to significant improvements over time. Organizations should strive to constantly refine and optimize their workflows, practices, and systems.
- Employee Involvement and EmpowermentTQM requires active participation from all employees. In a TQM-focused organization, employees at all levels are encouraged to identify problems, suggest improvements, and take responsibility for ensuring quality in their tasks. Empowering employees creates a culture of ownership and accountability.
- Process-Centered ApproachTQM emphasizes the importance of processes over individuals in achieving quality outcomes. The organization is viewed as a collection of interrelated processes, and improving the efficiency and effectiveness of these processes is essential for delivering quality products or services. Mapping and optimizing key processes is a central component of TQM.
- Integrated SystemIn a TQM system, all functions, departments, and employees work together toward a common goal of quality. Organizations must ensure that their business processes are integrated and aligned to support quality objectives. Often, this involves breaking down silos between departments to encourage collaboration.
- Fact-Based Decision MakingTQM advocates the use of data and analysis to guide decision-making. Decisions about quality improvement should be grounded in empirical evidence and data-driven insights. By leveraging tools like statistical process control, organizations can identify trends, detect variations, and determine root causes of problems.
- Strategic and Systematic ApproachTQM involves the strategic alignment of quality goals with organizational objectives. A systematic approach ensures that quality is embedded in the company’s long-term planning, resource allocation, and operations. This principle aligns with management by objectives (MBO), ensuring that quality improvement aligns with overall business strategies.
- Mutually Beneficial Supplier RelationshipsIn TQM, the quality of a company’s suppliers has a direct impact on the quality of the end product. Organizations must develop strong partnerships with suppliers to ensure that quality materials and services are delivered consistently. This includes collaboration on quality standards and continuous improvement initiatives.
- Leadership CommitmentStrong leadership is crucial for the success of TQM. Leaders must be committed to fostering a culture of quality, driving quality initiatives, and providing the resources needed to achieve quality objectives. Leadership plays a key role in setting quality goals, inspiring employees, and ensuring accountability.
Tools and Techniques in Total Quality Management
TQM employs a variety of tools and techniques to analyze processes, identify problems, and implement improvements. Some of the most widely used tools in TQM include:
- Pareto Analysis (80/20 Rule)
Pareto analysis is based on the principle that 80% of problems are often caused by 20% of the causes. This tool helps prioritize quality improvement efforts by focusing on the most significant factors contributing to quality issues. - Fishbone Diagram (Ishikawa Diagram)
The Fishbone diagram is a cause-and-effect tool used to identify potential causes of a specific problem. It categorizes causes into areas such as materials, methods, equipment, and people, helping teams analyze and resolve complex quality issues. - Control Charts
Control charts are used to monitor process performance over time. By plotting data points and analyzing variations, organizations can determine whether processes are stable and capable of producing quality outcomes. Control charts are a key component of statistical process control (SPC). - Failure Mode and Effects Analysis (FMEA)
FMEA is a proactive tool used to identify potential failure modes in a process and assess their impact on overall performance. It allows organizations to take preventive actions to mitigate risks before they affect quality. - Root Cause Analysis
Root Cause Analysis (RCA) is used to identify the underlying causes of a quality problem. Techniques like the 5 Whys help teams dig deep into an issue to uncover the root cause rather than just addressing symptoms. - Six Sigma
Six Sigma is a data-driven methodology that focuses on reducing defects and variability in processes. It uses the DMAIC (Define, Measure, Analyze, Improve, Control) framework to guide quality improvement projects. Many TQM organizations incorporate Six Sigma principles to achieve higher levels of process performance. - Quality Function Deployment (QFD)
QFD is a tool that helps translate customer needs and requirements into specific product or service features. It uses a matrix called the House of Quality to align customer expectations with product design and development.
Benefits of Total Quality Management
Organizations that successfully implement TQM can experience a wide range of benefits that extend beyond just improved product quality. Key advantages include:
- Enhanced Customer Satisfaction
By focusing on customer needs and continuously improving processes, TQM helps organizations deliver products and services that consistently meet or exceed customer expectations. Satisfied customers are more likely to become repeat buyers, improving long-term business performance. - Improved Product Quality
TQM drives higher quality standards by ensuring that processes are designed to prevent defects, reduce variability, and promote consistency. The result is fewer defects, less rework, and a higher-quality product or service. - Increased Efficiency and Productivity
Through process optimization and waste reduction, TQM helps organizations operate more efficiently. This leads to cost savings, faster production times, and better resource utilization. Employees are empowered to work more effectively and identify opportunities for further improvement. - Reduced Costs
TQM helps organizations minimize the costs associated with poor quality, such as rework, scrap, recalls, and warranty claims. Additionally, by improving supplier relationships and reducing process inefficiencies, TQM can lower production costs. - Employee Engagement and Satisfaction
TQM fosters a culture of participation and empowerment, where employees are encouraged to take ownership of their work and contribute to quality improvements. This leads to higher levels of job satisfaction, motivation, and engagement. - Stronger Market Position
Organizations that consistently deliver high-quality products and services are more competitive in the marketplace. TQM can enhance an organization’s reputation, increase market share, and improve brand loyalty. - Compliance with Regulations and Standards
Many industries require adherence to specific quality standards (e.g., ISO 9001). TQM helps organizations comply with these regulations by integrating quality management into every aspect of their operations.
Challenges of Total Quality Management
While the benefits of TQM are significant, its implementation can be challenging. Some of the common challenges include:
- Cultural Resistance
Implementing TQM often requires a shift in organizational culture, which can be met with resistance. Employees may be skeptical of new processes or hesitant to change long-established workflows. - Leadership Commitment
TQM requires strong and sustained commitment from leadership. Without the support of top management, quality initiatives may lose momentum or fail to receive the necessary resources. - Cost and Time Investments
The implementation of TQM can be resource-intensive, especially in the early stages. It requires investments in training, process re-engineering, and technology. The return on investment (ROI) may take time to materialize. - Integration with Existing Systems
For organizations with established systems and processes, integrating TQM can be complex. It may require significant adjustments to current workflows and the alignment of different departments. - Measurement and Accountability
Successfully measuring quality improvements and holding teams accountable for results can be difficult. Organizations must establish clear metrics and a culture of accountability to ensure the effectiveness of TQM.
Best Practices for Implementing Total Quality Management
- Strong Leadership Commitment
Ensure that leadership is fully committed to the principles of TQM and is willing to provide the resources needed for its success. Leaders should also set an example by promoting a culture of continuous improvement. - Employee Involvement
Engage employees at all levels by encouraging participation in quality improvement initiatives. Training and empowerment are essential to getting buy-in and creating a sense of ownership among staff. - Focus on the Customer
Keep the customer at the center of all quality improvement efforts. Gather feedback, analyze customer complaints, and ensure that products and services meet customer expectations. - Use Data and Metrics
Leverage data to guide decision-making and measure progress. Use key performance indicators (KPIs) to track improvements and identify areas for further optimization. - Foster a Culture of Continuous Improvement
Create an environment where employees are encouraged to identify problems, suggest improvements, and continuously refine processes. Celebrate small wins to reinforce the importance of ongoing improvement. - Start Small, Scale Up
Implement TQM gradually, starting with pilot projects in specific areas of the organization. Once successes are achieved, scale up the initiative to cover more departments and processes.
Conclusion
Total Quality Management is a powerful management philosophy that promotes a culture of continuous improvement, customer satisfaction, and organizational excellence. By integrating quality into every aspect of the business, TQM enables organizations to deliver superior products and services while reducing costs and increasing efficiency.
While implementing TQM comes with challenges, organizations that commit to its principles and foster a culture of quality can achieve long-term success and maintain a competitive edge in the market. Through strong leadership, employee involvement, and a focus on process improvement, TQM offers a proven path to enhanced organizational performance.