Quality Management Software For Manufacturing
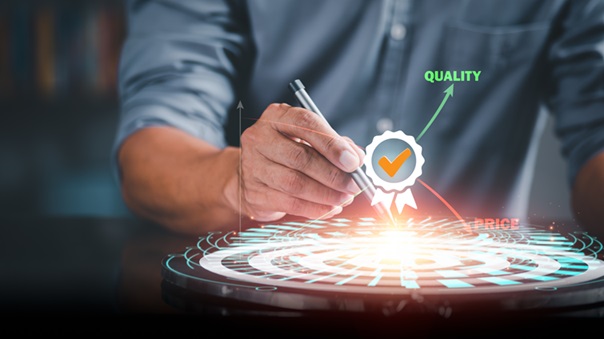
In today's highly competitive manufacturing landscape, quality management is critical to success. Quality Management Software (QMS) for manufacturing has become indispensable for ensuring that products meet customer expectations while adhering to regulatory requirements and industry standards. This guide explores the essential features, benefits, implementation strategies, and challenges associated with QMS in manufacturing.
What is Quality Management Software (QMS)?
Quality Management Software is a digital solution designed to manage, monitor, and improve the quality processes in an organization. In the context of manufacturing, QMS integrates various quality control functions into a centralized system, enabling manufacturers to streamline processes, reduce errors, and ensure compliance with regulatory standards. QMS is essential for maintaining product quality throughout the production lifecycle, from raw material sourcing to final product delivery.
Importance of QMS in Manufacturing
In manufacturing, maintaining high quality is not just about meeting customer expectations; it also directly affects a company's bottom line. Poor quality control can lead to product recalls, rework, customer dissatisfaction, and ultimately lost revenue. Moreover, in industries like automotive, aerospace, and pharmaceuticals, quality control is regulated by stringent standards such as ISO 9001, FDA guidelines, or AS9100. Failure to comply with these standards can result in significant penalties, loss of certification, and damage to brand reputation.
A robust QMS ensures that all quality-related processes are optimized, standardized, and continuously improved. It allows for real-time monitoring of production, enabling manufacturers to identify and address issues before they escalate into costly problems.
Core Features of Quality Management Software for Manufacturing
QMS solutions for manufacturing typically include several core modules that help manage various aspects of quality control. These features vary depending on the software, but the most common ones are:
- Document Control
Document control ensures that all quality-related documents, such as work instructions, standard operating procedures (SOPs), and specifications, are up-to-date, accessible, and compliant with relevant regulations. With QMS, documents are stored in a centralized digital repository, allowing authorized personnel to access the latest versions and track changes efficiently. - Corrective and Preventive Actions (CAPA)
CAPA is a critical feature that helps manufacturers address quality issues systematically. QMS helps in identifying the root cause of defects or non-conformances, implementing corrective measures to prevent recurrence, and monitoring the effectiveness of those actions. CAPA modules provide real-time insights, helping teams make data-driven decisions to mitigate risks. - Audit Management
Regular audits are essential for ensuring compliance with quality standards and identifying areas for improvement. QMS includes tools for planning, scheduling, and executing internal and external audits. Audit findings can be tracked, and corrective actions can be assigned and monitored through the software, ensuring that issues are resolved promptly. - Supplier Quality Management (SQM)
In manufacturing, supplier quality is as important as in-house quality control. Poor-quality raw materials can lead to defective final products. QMS includes supplier management tools that help manufacturers evaluate and monitor supplier performance, ensuring that materials and components meet required standards. The software can track supplier certifications, audits, and non-conformance issues. - Non-conformance Management
When a product or process fails to meet predefined quality standards, a non-conformance report (NCR) is generated. QMS helps streamline the process of identifying, documenting, and resolving non-conformances. The software provides a structured workflow for managing NCRs, including assigning responsibility, tracking resolution status, and implementing preventive actions. - Statistical Process Control (SPC)
SPC tools within QMS enable manufacturers to monitor and control production processes using real-time data. By analyzing data from production lines, manufacturers can identify trends, variances, and potential issues before they lead to defects. SPC helps in maintaining process stability and improving overall product quality. - Risk Management
QMS helps manufacturers assess and manage risks associated with quality processes. This includes identifying potential hazards, evaluating their impact on operations, and implementing controls to mitigate risks. Risk management tools within QMS allow for proactive quality management, helping companies avoid costly mistakes and non-compliance penalties. - Training Management
Ensuring that employees are properly trained on quality processes, equipment, and standards is crucial in manufacturing. QMS includes training management modules that allow manufacturers to track employee certifications, schedule training sessions, and ensure that personnel remain compliant with industry regulations and company policies. - Compliance Management
Compliance with industry regulations and standards such as ISO 9001, ISO 13485, and FDA guidelines is a critical aspect of quality management in manufacturing. QMS helps companies maintain compliance by providing tools to track regulatory changes, manage certifications, and automate compliance reporting.
Benefits of Implementing QMS in Manufacturing
- Enhanced Product Quality
The primary goal of QMS is to improve product quality by identifying and eliminating defects and inefficiencies in the production process. By integrating quality control tools such as SPC, CAPA, and non-conformance management, manufacturers can consistently deliver high-quality products that meet customer expectations. - Increased Operational Efficiency
QMS helps manufacturers streamline their quality processes, reducing the time and effort required to manage quality control activities. By automating tasks such as document management, audit scheduling, and supplier evaluations, QMS allows quality teams to focus on more strategic initiatives. This leads to improved productivity and reduced operational costs. - Regulatory Compliance
Compliance with industry regulations and standards is mandatory for manufacturers in highly regulated industries. QMS ensures that all processes, documents, and records are compliant with the latest regulatory requirements, reducing the risk of non-compliance penalties and certification loss. - Improved Data Visibility
One of the key advantages of QMS is the ability to provide real-time insights into quality performance. With centralized data collection and reporting capabilities, manufacturers can monitor quality metrics such as defect rates, supplier performance, and process variability. This data-driven approach helps in making informed decisions and driving continuous improvement. - Cost Savings
By reducing the occurrence of defects, rework, and product recalls, QMS helps manufacturers save on costs associated with poor quality. Additionally, by improving operational efficiency and reducing downtime, QMS contributes to overall cost reductions. - Better Supplier Relationships
QMS enables manufacturers to evaluate and monitor supplier performance more effectively, ensuring that raw materials and components meet quality standards. This leads to stronger supplier relationships, as manufacturers can collaborate with their suppliers to improve quality and reduce lead times. - Risk Mitigation
QMS provides tools for proactive risk management, helping manufacturers identify potential quality issues before they escalate into major problems. By addressing risks early in the production process, companies can avoid costly recalls, customer complaints, and damage to their reputation.
Challenges in Implementing QMS for Manufacturing
Despite the numerous benefits, implementing a QMS in manufacturing is not without challenges. Some of the common challenges include:
- Change Management
Introducing a new QMS often requires significant changes in the way employees work. Resistance to change can be a major hurdle in the successful implementation of the software. To overcome this, manufacturers need to invest in employee training, change management strategies, and leadership support. - Integration with Existing Systems
Many manufacturers already have legacy systems in place, such as ERP (Enterprise Resource Planning) or MES (Manufacturing Execution System). Integrating a new QMS with these systems can be complex and time-consuming. It is essential to choose a QMS that offers seamless integration capabilities with existing software to avoid data silos and ensure a smooth transition. - Cost of Implementation
While QMS offers significant long-term benefits, the initial cost of implementation can be high. This includes the cost of purchasing the software, customizing it to fit the organization's needs, and training employees. However, the return on investment (ROI) is typically realized over time through improved product quality, reduced waste, and increased efficiency. - Regulatory Complexity
Manufacturing companies operating in multiple countries often face the challenge of complying with different regulatory requirements in each region. A QMS must be flexible enough to accommodate these varying regulations while ensuring global compliance. - Customization Needs
Every manufacturing process is unique, and a one-size-fits-all QMS may not meet the specific needs of every organization. Customizing the software to fit unique workflows, processes, and standards can be a time-consuming and costly process.
Best Practices for Implementing QMS in Manufacturing
- Conduct a Thorough Needs Assessment
Before implementing a QMS, manufacturers should conduct a thorough needs assessment to identify gaps in their current quality processes and determine the specific features and functionalities required in a QMS. This helps in selecting the right software that aligns with the organization's goals and objectives. - Choose a Scalable QMS
Manufacturing companies should choose a QMS that can scale with their business as it grows. A scalable QMS allows companies to add new modules, users, and locations as needed, without the need for a complete system overhaul. - Involve Cross-Functional Teams
Successful QMS implementation requires input from various departments, including quality, production, engineering, and IT. Involving cross-functional teams in the selection, customization, and implementation of the QMS ensures that all stakeholders' needs are addressed and that the system integrates seamlessly into existing workflows. - Provide Comprehensive Training
Employee training is critical to the success of a QMS implementation. Manufacturers should provide comprehensive training to all employees who will be using the software, ensuring they understand its features and how to use it effectively in their daily work. - Monitor and Continuously Improve
QMS is not a one-time implementation but a continuous process. Manufacturers should regularly monitor the system's performance, track key quality metrics, and make necessary adjustments to improve processes. Continuous improvement is essential for staying competitive in today's dynamic manufacturing environment.
The Future of QMS in Manufacturing
As manufacturing continues to evolve with advancements in Industry 4.0 technologies, such as the Internet of Things (IoT), artificial intelligence (AI), and big data, QMS is also expected to become more sophisticated. The future of QMS in manufacturing will likely include enhanced predictive analytics, real-time monitoring, and more seamless integration with smart manufacturing technologies.
For example, IoT-enabled QMS can collect real-time data from connected machines and sensors on the shop floor, allowing manufacturers to monitor quality metrics more closely and take immediate corrective action when deviations are detected. AI-driven QMS can provide predictive insights, helping manufacturers anticipate potential quality issues before they occur and implement preventive measures proactively.
Conclusion
Quality Management Software is a critical tool for manufacturers looking to maintain high standards of product quality, comply with industry regulations, and improve operational efficiency. By centralizing and automating quality processes, QMS helps manufacturers reduce defects, mitigate risks, and drive continuous improvement. While the implementation of QMS may come with challenges, the long-term benefits far outweigh the initial costs, making it a worthwhile investment for any manufacturing organization looking to stay competitive in today's market.
With the continuous advancement of technology, the future of QMS in manufacturing looks promising, with more sophisticated tools and features that will further enhance quality management capabilities. Manufacturers that embrace these technologies will be well-positioned to deliver high-quality products, improve customer satisfaction, and achieve sustained success in the industry.