Quality Control Seven Tools
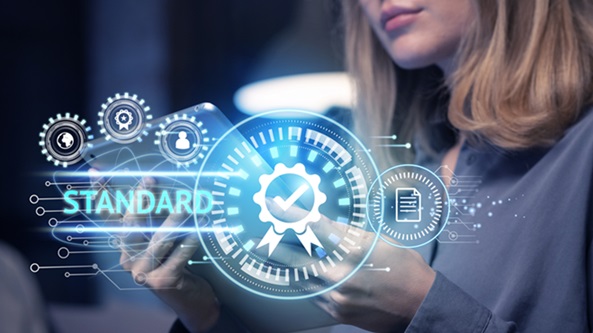
The Seven Tools of Quality Control, also known as the Seven Quality Control Tools, are instrumental in process improvement, problem-solving, and quality management. Originating from Japan after World War II, these tools became a central element of Total Quality Management
(TQM) and were adopted widely in the industrial sector. They are simple to use, highly effective, and suitable for workers at every level in an organization, helping teams identify and solve problems related to quality. Let's delve into each of these seven tools, covering their features, benefits, applications, and how they support quality management initiatives.
1. Cause-and-Effect Diagram (Ishikawa or Fishbone Diagram)
Overview:
The Cause-and-Effect Diagram, developed by Kaoru Ishikawa, is also known as the Fishbone Diagram because of its resemblance to a fish skeleton. It is used to systematically identify potential causes of a problem, particularly when dealing with complex issues. The goal is to drill down to the root cause of an issue rather than merely treating its symptoms.
Structure:
The diagram starts with the problem (effect) written on the right side of the chart. The main causes (such as machinery, materials, methods, and manpower) branch off the central spine like the bones of a fish. These major categories then break down into more specific contributing factors, creating a visual representation of possible root causes.
Benefits:
- Encourages a comprehensive examination of potential causes.
- Stimulates brainstorming and collaboration within teams.
- Helps in categorizing causes and identifying relationships between them.
- Particularly useful in root cause analysis and process improvement.
Application:
Used in industries ranging from manufacturing to healthcare, this tool helps teams tackle issues like process failures, production defects, or service delays. For instance, in manufacturing, the categories might include machine performance, operator skills, environmental conditions, and raw materials.
2. Check Sheet
Overview:
A Check Sheet is a structured form for collecting and analyzing data. It is used to systematically record information in real time at the location where the data is generated. This tool is versatile and can be used for various purposes, such as tracking defects, documenting frequencies of events, or counting occurrences of activities.
Structure:
Check Sheets are typically simple forms that are easy to design. They feature columns for recording different types of information, such as the date, description of defects, number of occurrences, or types of problems. They can also include spaces for tally marks, making it easy to visualize data trends.
Benefits:
- Encourages data-driven decision-making.
- Helps in identifying patterns or trends over time.
- Easy to implement and customize based on specific needs.
- Reduces errors by providing a standardized way of collecting data.
Application:
Check Sheets are often used in quality control processes to monitor defect rates, equipment breakdowns, or customer complaints. For example, a manufacturing company might use a Check Sheet to record defects during the production process to monitor product quality and take corrective action where necessary.
3. Control Chart
Overview:
A Control Chart is a powerful tool used in Statistical Process Control (SPC) to monitor process behavior over time. It helps in determining whether a process is stable and operating within control limits or if it has become unpredictable due to variations. Control Charts differentiate between common cause variations (natural to the process) and special cause variations (indicating something has gone wrong).
Structure:
The chart features a central line representing the process average, with upper and lower control limits set based on historical data. Data points are plotted over time, and the chart can reveal whether the process is in control (within limits) or if corrective action is needed (when points fall outside the limits).
Benefits:
- Provides real-time insight into process stability.
- Identifies process trends or shifts before defects occur.
- Helps in reducing variation and improving process consistency.
- Facilitates early intervention and continuous improvement.
Application:
Control Charts are frequently used in manufacturing processes to monitor production quality and maintain consistent product specifications. For example, in a bottling plant, a Control Chart might track the volume of liquid dispensed into bottles to ensure it stays within acceptable limits.
4. Histogram
Overview:
A Histogram is a graphical representation of data distribution. It shows how data is spread over different intervals, providing a clear view of the frequency of data points within each range. A Histogram is valuable for understanding variation in a dataset, identifying patterns, and determining the distribution type (normal, skewed, etc.).
Structure:
A Histogram consists of bars representing frequency counts of data points within specific intervals. The height of each bar corresponds to the number of occurrences within that interval. The x-axis represents the data intervals, while the y-axis shows the frequency of occurrences.
Benefits:
- Visualizes data distribution in an easy-to-understand format.
- Highlights areas where defects or variations are concentrated.
- Useful for identifying patterns, outliers, or anomalies.
- Facilitates comparison of different data sets.
Application:
Histograms are often used in quality control to analyze the distribution of defects, production times, or any measurable characteristic of a process. For example, a manufacturing plant might use a Histogram to visualize the frequency of product defects by size, allowing them to determine whether their production process is skewed or operating within the desired range.
5. Pareto Chart
Overview:
The Pareto Chart is a bar graph that follows the Pareto Principle, also known as the 80/20 rule, which states that 80% of problems are caused by 20% of the factors. The chart helps prioritize issues by showing which factors are most significant, allowing teams to focus their efforts on addressing the major contributors to a problem.
Structure:
A Pareto Chart features bars that represent the frequency or impact of different problems, arranged in descending order of significance. A cumulative line is often added to the chart to show the combined effect of all factors. The bars on the left represent the highest-impact problems, helping teams to identify where they should concentrate their efforts.
Benefits:
- Helps prioritize problems and focus on critical issues.
- Provides a clear visual representation of the most significant factors.
- Facilitates efficient use of resources by focusing on high-impact areas.
- Encourages data-driven decision-making and problem-solving.
Application:
In quality management, Pareto Charts are commonly used to prioritize defects, customer complaints, or production issues. For example, a customer service department might use a Pareto Chart to analyze the types of complaints they receive, enabling them to address the top issues affecting customer satisfaction.
6. Scatter Diagram
Overview:
A Scatter Diagram, also known as a scatter plot or scatter graph, is used to study the relationship between two variables. It helps to determine whether there is a correlation between variables and, if so, whether the relationship is positive, negative, or nonexistent. This tool is especially useful in identifying cause-and-effect relationships.
Structure:
The Scatter Diagram consists of a series of data points plotted on a graph, with one variable on the x-axis and the other on the y-axis. The pattern of points on the chart indicates whether the variables are correlated. A positive correlation is indicated by an upward-sloping pattern, while a negative correlation is indicated by a downward slope. If the points are scattered randomly, it suggests no correlation between the variables.
Benefits:
- Helps in identifying correlations and relationships between variables.
- Facilitates understanding of cause-and-effect dynamics.
- Provides a visual method for analyzing data trends.
- Assists in predicting outcomes based on variable relationships.
Application:
Scatter Diagrams are often used in manufacturing to explore the relationship between different process variables. For example, a Scatter Diagram might be used to determine the correlation between machine speed and defect rate. By analyzing the diagram, the company could adjust machine speed to reduce defects and improve product quality.
7. Flowchart
Overview:
A Flowchart is a visual representation of a process, showing each step in sequential order. It is used to map out processes, allowing teams to analyze and improve workflow, identify bottlenecks, and streamline operations. Flowcharts are easy to understand and can be used to communicate complex processes in a simple format.
Structure:
Flowcharts consist of various symbols, such as rectangles (for process steps), diamonds (for decision points), and arrows (to indicate the flow of the process). Each symbol represents a different type of action or decision, with arrows connecting them to illustrate the flow of activities from one step to the next.
Benefits:
- Provides a clear, visual representation of processes.
- Identifies bottlenecks, redundancies, or inefficiencies.
- Facilitates communication and understanding among team members.
- Supports process improvement and standardization efforts.
Application:
Flowcharts are widely used in industries like manufacturing, healthcare, and IT to map out processes and identify areas for improvement. For instance, a company might use a Flowchart to diagram the steps involved in their product assembly process, making it easier to identify inefficiencies and improve overall workflow.
Importance of the Seven Tools of Quality Control in Quality Management
The Seven Quality Control Tools are foundational for improving quality within any organization, providing teams with the means to control processes, detect problems, and drive continuous improvement. They have been proven to be highly effective when implemented as part of a broader quality management system like Total Quality Management (TQM) or Six Sigma. Here are some key reasons why these tools are essential:
- Promote Data-Driven Decision-Making: Each of these tools emphasizes the importance of data collection and analysis, enabling organizations to make informed decisions based on objective evidence rather than assumptions.
- Enable Root Cause Analysis: Tools like the Fishbone Diagram and Scatter Diagram help teams delve into the underlying causes of problems, leading to more effective solutions.
- Facilitate Continuous Improvement: Whether used in daily operations or major projects, these tools support the Plan-Do-Check-Act (PDCA) cycle and the pursuit of continuous improvement