Difference Between Quality Control And Quality Assurance
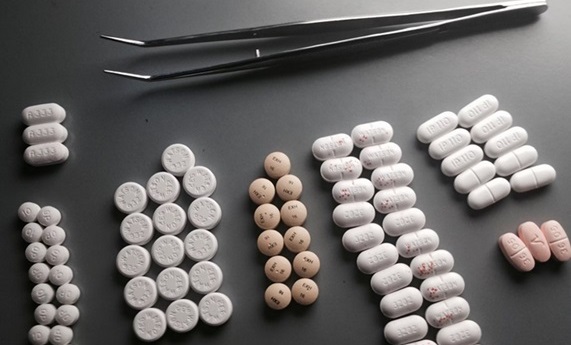
Introduction
Quality is a critical component in any industry, but it holds particular significance in sectors like pharmaceuticals, manufacturing, and software development, where product quality directly impacts safety, functionality, and customer satisfaction. Two fundamental concepts that underpin the management of quality in these industries are Quality Assurance (QA) and Quality Control (QC). Although they are often used interchangeably, QA and QC are distinct processes with unique roles in ensuring product quality.
This article will provide an in-depth exploration of Quality Assurance and Quality Control, highlighting their differences, how they interrelate, and their importance in maintaining high standards in product development and manufacturing.
1. Understanding Quality Assurance (QA)
Quality Assurance (QA) refers to the proactive process that ensures quality is built into every stage of product development or service delivery. It encompasses the systematic activities implemented within the quality management system to ensure that processes are adequate to achieve the required quality levels. QA is about preventing defects and ensuring that the processes used to create a product or service are sufficient to meet quality standards.
Key aspects of Quality Assurance include:
Process-Oriented Approach:
QA is fundamentally process-oriented. It focuses on improving and stabilizing production processes to minimize the chances of defects. By refining the processes, QA aims to ensure that the final product meets the required quality standards before it reaches the customer.Standards and Compliance:
QA involves developing and maintaining documented procedures and standards that align with regulatory requirements and industry best practices. This includes establishing protocols, work instructions, and guidelines that must be followed during production or service delivery.Continuous Improvement:
Quality Assurance is not a one-time activity but an ongoing effort. It includes regular audits, process reviews, and the implementation of corrective and preventive actions (CAPA) to continuously improve processes and maintain consistent quality.Employee Training:
Ensuring that employees are adequately trained in the relevant processes and quality standards is a critical component of QA. Well-trained employees are less likely to make errors, contributing to the overall quality of the product.Documentation and Records:
QA requires meticulous documentation of all processes, procedures, and quality checks. This documentation serves as evidence of compliance and provides a basis for process improvements.
2. Understanding Quality Control (QC)
Quality Control (QC) is the process of inspecting products to ensure they meet the specified quality standards. Unlike QA, which is process-oriented, QC is product-oriented, focusing on identifying and correcting defects in the final products. QC involves testing, inspection, and review activities to verify that the output of a production process meets the established criteria.
Key aspects of Quality Control include:
Product-Oriented Approach:
QC is primarily concerned with examining and testing the final product. This might include checking the physical properties, performance, and functionality of a product to ensure it meets the defined specifications and standards.Inspection and Testing:
QC activities often involve detailed inspection and testing of products. This can range from simple visual inspections to complex testing procedures that assess various attributes of the product. For example, in manufacturing, this could involve dimensional checks, material analysis, or functionality tests.Defect Identification and Correction:
The primary goal of QC is to identify any defects or deviations from the specified quality standards. Once a defect is identified, corrective actions are taken to rectify the issue, either by reworking the product or scrapping it altogether.Sampling Techniques:
In many industries, it is impractical to inspect every single product. Therefore, QC often employs sampling techniques, where a representative sample of products is tested. The results from these samples are used to infer the quality of the entire batch.Feedback Loop:
Quality Control provides critical feedback to the production process. Information about defects or inconsistencies is fed back to the QA process, helping to refine and improve the production processes over time.Documentation:
Similar to QA, QC also involves detailed documentation, particularly concerning the results of inspections and tests. These records are essential for traceability, regulatory compliance, and continuous improvement efforts.
3. Key Differences Between Quality Assurance and Quality Control
Although Quality Assurance and Quality Control are both integral to ensuring quality, they differ in several key areas:
Focus and Orientation:
QA:
QA is focused on the process and is proactive in nature. It aims to prevent defects by improving the processes involved in creating the product. QA is concerned with building quality into the processes.
QC:
QC is focused on the product and is reactive. It seeks to identify and correct defects in the final product. QC ensures that the product meets the quality standards before it reaches the customer.
Approach:
QA:
QA takes a systematic and preventive approach, aiming to build quality into the process from the beginning. This approach involves establishing robust processes, procedures, and standards.
QC:
QC is an inspection-based approach. It involves checking the final product against predefined criteria and standards, identifying defects after the product has been produced.
Timing:
QA:
QA activities are conducted throughout the production process, from the initial design phase to final delivery. QA is ongoing and continuous, with the aim of preventing defects before they occur.
QC:
QC activities are performed at specific points, typically at the end of the production process or during certain phases where testing and inspection are necessary. QC is focused on detecting defects after they have occurred.
Objective:
QA:
The objective of QA is to ensure that the processes used to develop or produce a product are adequate and capable of producing a quality product. QA is about process optimization and risk management.
QC:
The objective of QC is to ensure that the final product meets the quality standards and is free from defects. QC is about verifying that the product is ready for delivery to the customer.
Responsibility:
QA:
QA is typically the responsibility of a dedicated QA team that works closely with various departments, including production, R&D, and management, to develop and implement quality systems.
QC:
QC is often the responsibility of a QC team or department, which may work independently or as part of the production team, focusing on testing and inspection activities.
Outcome:
QA:
The outcome of QA is improved processes, reduced risk of defects, and greater consistency in product quality. QA aims to minimize the occurrence of defects by refining processes.
QC:
The outcome of QC is the identification and correction of defects in the product, ensuring that only products that meet the quality standards are delivered to the customer.
Methods and Tools:
QA:
QA uses tools like process audits, CAPA (Corrective and Preventive Actions), process flowcharts, and quality management software to ensure process integrity and continuous improvement.
QC:
QC uses tools like statistical quality control (SQC), inspection checklists, sampling methods, and testing equipment to assess product quality.
4. How QA and QC Work Together
Despite their differences, Quality Assurance and Quality Control are closely interrelated and work together to achieve the common goal of ensuring product quality. Their relationship can be understood as complementary, with each playing a critical role in the quality management process.
Mutual Feedback Loop:
QA and QC operate in a feedback loop where information from QC activities is used to improve QA processes. For instance, defects identified during QC can highlight weaknesses in the production process, leading to adjustments in the QA procedures to prevent future occurrences.
Sequential Relationship:
In a typical workflow, QA activities occur before QC activities. QA ensures that processes are set up correctly and that quality is built into the production from the start. QC then comes into play at the end of the production process, verifying that the outputs meet the quality criteria.
Continuous Improvement:
Both QA and QC contribute to the continuous improvement of quality management systems. While QA focuses on process improvement, QC provides the data and insights needed to guide these improvements, creating a cycle of ongoing enhancement.
Shared Goal:
Ultimately, both QA and QC aim to deliver a product that meets or exceeds customer expectations and complies with relevant regulatory standards. By working together, they ensure that quality is not just a final check but a fundamental aspect of the entire production process
Visit our Service:https://likeways.co.in/resume-build-and-review/