Corrective And Preventive Action Plan (Capa)
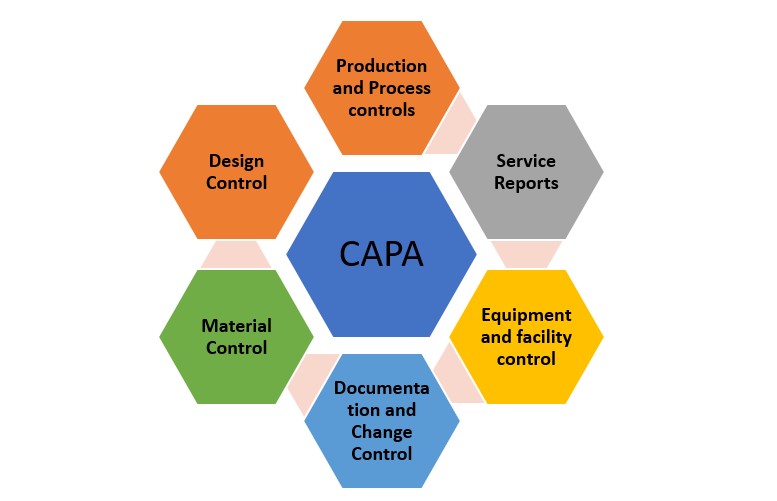
1.0 PURPOSE:
This procedure ensures that discrepancies in GMP compliance/quality systems are investigated, corrective actions are taken to eliminate the root causes of non-conformances, and preventive actions are taken to eliminate the causes of potential non-conformances.
2.0 SCOPE:
This procedure applies to the implementation of corrective actions and preventive actions resulting from the investigation of following non-conformances in manufacturing and testing activities.
A) Internal Data/Records
1. Deviation Reports
2. Self-Inspection/Internal Audit Reports
3. In-process / Inspection Results...etc
4. Risk Assessment and Findings
5. Change Control Reports
6. Annual / Quarterly trends of QMS Documents
7. Product Quality Review
8.OOS/OOT
9. Laboratory Deviations
10. Training...etc
B) External Data
1. Market
2. Service Reports
3. Product Recall
3.0 RESPONSIBILITIES:
All Departments Heads
4.0 DEFINITIONS:
4.1 Corrective Action:
Action is taken to eliminate the causes of a detected non-conformance, defect or other undesirable situations to prevent recurrence.
4.2 Preventive Action:
Action is taken to eliminate the cause of the potential non-conformance, defect, or other undesirable situations to prevent occurrence.
4.3 CAPA (Corrective and Preventive Action):
A systematic approach includes actions needed to correct (correct), prevent recurrence (corrective action), and eliminate the cause of potential (preventive action), non-conforming products, and other quality problems.
4.4 Discrepancy: Data or results outside of the expected range; an unfulfilled requirement, may be called non-conformity, defect, deviation, out-of-specification, laboratory deviation, or out-of-trend.
5.0 PROCEDURE:
5.1 CAPA shall be initiated based on the investigation of the discrepancies reported related to the process, procedure, and systems, "Scope" of this procedure to prevent the occurrence and reoccurrence of the existing discrepancies/deficiencies.
5.2 CAPA shall be proposed after conducting a comprehensive root-cause analysis in relevant procedures for handling discrepancies. A multi-disciplinary team comprising persons involved in the process during the occurrence of the discrepancy (from the Originating department) and/or personnel from other departments affected by the discrepancy and Site QA personnel shall perform the Root Cause Analysis.
5.3 CAPA shall be initiated if the review of the trend of internal or external data of the systems/procedures, indicates any repeat deficiency or an adverse trend potentially impacting the quality system or quality of the product.
5.4 For ease of handling CAPA system is divided into three phases.
Phase I-Initiation, Assessment, and Approval of CAPA
Phase II-Implementation of CAPA, Review of Implemented CAPA, and Closure of CAPA
Phase III-CAPA Effectiveness Monitoring and Closure
5.4.1 Phase I - Includes initiation of CAPA along with the action plan for the activities to be completed, CAPA effectiveness monitoring plan, review and approval of CAPA.
5.4.2 Phase II - Includes implementation of CAPA within the target timeline, training to target group, Controlled review of implementation, and closure of CAPA.
5.4.3 Phase III Effectiveness monitoring to confirm the quality objectives are achieved for the CAPA implemented system and closure.
5.5 Timeline for Implementation of CAPA:CAPA shall be implemented within 30 working days of the approval of the proposal. However, based on the nature of the CAPA and, the extent of the work and activities involved, if more than 30 days are required, the Originating department head shall specify the number of days required for implementation along with the justification
5.6 Review of Implemented CAPA: Each identified activity which are listed in "Action Plan for Implementation of Proposed,shall be reviewed by the Head of the Originating department and shall mention the date of completion in the form.
5.6.1 Site QA shall verify the implemented CAPA by reviewing the activities identified during the assessment of CAPA and the applicable documents.
5.8 Closure of CAPA Implementation: CAPA implementation shall be closed by the Site QA Head within 7 working days from the date of completion of identified activities.
5.9 CAPA Effectiveness Monitoring and Closure: After the implementation of CAPA, an evaluation shall be undertaken to confirm the quality objectives are achieved and that there is no unintended deleterious impact on product quality.
5.9.1 Based on the CAPA effectiveness monitoring plan, Site QA shall verify the effectiveness of the implementation of CAPA to ascertain whether the changes and the consequent changes have been implemented satisfactorily by reviewing the executed activities and documents such as qualification reports, analytical data, logbooks, validations, validation reports, training records etc. For the identified GAPS if actions are to be taken, responsibility, target completion date, and remarks if any shall be recorded by the Head of the Originating department in consultation with the Head of Site QA.
5.9.2 If additional CAPA is identified based on review and monitoring, the same shall be implemented after carrying out a risk assessment of the additional CAPA proposed.
6.0 REFERENCE:
6.1 ICH Q10-Pharmaceutical Quality System
6.2 Change Control System
6.3 Quality System Review
6.4 Root Cause Analysis
7.0 ABBREVIATIONS:
7.1 GMP: Good Manufacturing Practices
7.2 OOS: Out of Specification
Get ready to use editable documents in MS Word Format (Regulatory standard SOPs with Formats,Templates and Annexure) Only Rs-99₹/-
Contact:
Email: contact@likeways.co.in
WhatsApp/Telegram No: 9738137533 (Only for Message)
Note: Kindly note that you will receive the document through email only after the payment has been completed. Please send the screenshot of your payment confirmation via WhatsApp/Telegram. A payment QR code will be provided from our end.