5 Whys Root Cause Analysis And Template
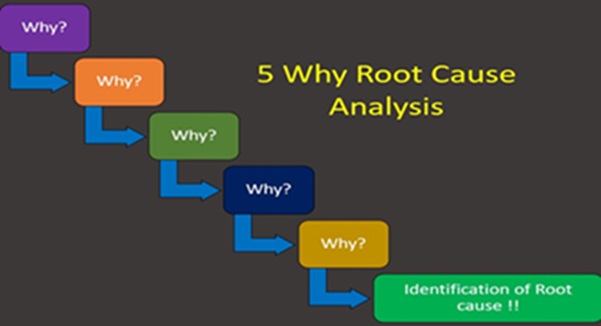
Introduction
The 5 Whys Root Cause Analysis might be the solution you've been looking for. This problem-solving technique is like peeling an onion to get to the core of the problem, rather than just dealing with surface-level symptoms. Whether you work in manufacturing, service, or any other industry, the 5 Whys Technique can help you uncover the underlying causes of recurring issues. In this report, we will delve into the world of root cause analysis, exploring its process, benefits, limitations, and real-world applications. Get ready to unravel the mysteries behind those nagging problems and discover the power of asking "why."
Understanding the 5 Whys Technique
Getting to the Root of the Issue
Have you ever found yourself scratching your head over a problem that just won't seem to disappear? The 5 Whys Technique is like a detective, guiding you through a series of "whys" to uncover the root cause of an issue. By peeling away the layers of symptoms and getting to the core problem, this method helps you tackle issues at their source. It's not about slapping on a band-aid; it's about diving deep and finding lasting solutions.
Uncovering Hidden Causes
Imagine you're dealing with a recurring problem at work - a glitch in the system, a breakdown in communication, or a persistent error. Instead of simply fixing the immediate issue, the 5 Whys Technique prompts you to ask "why" repeatedly. This process of drilling down into the underlying causes can reveal hidden factors that may have been overlooked. It's like unraveling a tangled knot to find the loose end that, once pulled, resolves the entire mess.
Going Beyond the Surface
At first glance, a problem may seem straightforward, but the 5 Whys Technique challenges you to look beyond the surface. By delving into the "whys" behind the problem, you may uncover interconnected issues, systemic flaws, or overlooked details that contribute to the larger issue. This method encourages a holistic understanding of the problem, rather than just treating the symptoms. It's about addressing the cause, not just the effect.
Empowering Problem-Solving Skills
As you engage in the 5 Whys Technique, you're not just solving a problem – you're honing your critical thinking skills. By asking "why" repeatedly, you're training your mind to think analytically, to question assumptions, and to seek out underlying causes. This method empowers you to approach problems strategically, to see beyond the obvious, and to develop solutions that target the root of the issue. It's a valuable tool for problem-solving that can be applied across various industries and situations.
Benefits of the 5 Whys Technique
When it comes to problem-solving, the 5 Whys Technique offers a plethora of benefits that can transform the way you tackle issues in the workplace. By repeatedly asking "why," this approach gets to the heart of the problem, ensuring that you're not just addressing surface-level symptoms. This method is all about uncovering the true cause behind the issue, leading to more effective and long-lasting solutions.
One of the key advantages of the 5 Whys Technique is its simplicity and cost-effectiveness. Unlike complex statistical analyses or expensive tools, this approach is straightforward and easy to understand, requiring minimal resources. By encouraging critical thinking, the technique prompts individuals to explore underlying causes, assumptions, and biases, leading to a more comprehensive analysis. This not only aids in problem resolution but also fosters a culture of continuous improvement within the organization.
Moreover, the 5 Whys Technique helps prevent problem recurrence by targeting the root cause of the issue. This proactive approach results in long-term improvements in processes and systems, ultimately boosting efficiency and productivity. By promoting a continuous improvement mindset, this method encourages individuals to think beyond quick fixes and seek sustainable solutions. The iterative nature of the technique drives overall organizational growth and sets the stage for ongoing success.
Limitations of the 5 Whys Technique
When it comes to problem-solving, the 5 Whys Technique is a powerful tool, but it does have its limitations. One significant drawback is the subjective nature of the analysis process. Since it relies on human judgment and interpretation, there is a risk of introducing bias and potentially leading to incorrect or incomplete root cause identification. This subjectivity can sometimes cloud the true underlying issues, hindering the effectiveness of the solutions proposed.
In addition to subjectivity, the depth of analysis is another limitation to consider. While asking "why" multiple times can reveal valuable insights, it may not always lead to a deep enough understanding of complex problems. Some issues require a more thorough investigation beyond the five-question framework. In such cases, a more comprehensive approach may be necessary to ensure a holistic understanding of all contributing factors.
Furthermore, the lack of data-driven analysis is a notable limitation of the 5 Whys Technique. This method primarily relies on qualitative analysis and does not incorporate extensive data analysis or statistical techniques. While the simplicity of this approach has its benefits, it may limit the accuracy and reliability of the findings. In situations where data-driven insights are crucial, additional tools and methodologies may be needed to complement the 5 Whys analysis.
Lastly, the time-consuming nature of conducting a thorough 5 Whys analysis is a practical limitation to consider. For complex problems that require a deep dive into root causes, the iterative nature of this technique can be resource-intensive. This may pose challenges in time-sensitive situations where quick resolutions are needed. It's essential to weigh the benefits of in-depth analysis against the practical constraints of time and resources when deciding whether to apply the 5 Whys Technique.
Real-world Applications
The 5 Whys Technique finds applications in various industries and sectors, proving to be a valuable tool for problem-solving. In manufacturing settings, this technique is instrumental in identifying the root cause of product defects, equipment failures, or production delays. By addressing the underlying issues uncovered through the 5 Whys analysis, organizations can make significant process improvements and enhance product quality.
Moreover, the service industry also benefits from the application of the 5 Whys Technique. Service providers utilize this method to analyze customer complaints, service failures, and operational issues. By understanding the root cause of these issues, companies can implement targeted solutions that not only address the symptoms but also prevent the problem from recurring.
Beyond manufacturing and the service industry, the 5 Whys Technique has proven to be effective in the pharmaceutical sector. For instance, in the context of Clinical Research, this method aids in investigating deviations and failures, leading to enhanced protocol compliance and data integrity. By delving deep into the underlying causes of issues, organizations can make informed decisions that drive improvements in their processes.
In the realm of failure investigation, the 5 Whys Technique serves as a powerful tool for uncovering the root causes of failures in systems, processes, or products. This method enables organizations to go beyond quick fixes and address the fundamental issues that contribute to failures. By adopting a proactive approach to problem-solving, businesses can drive continuous improvement and prevent future failures, ultimately enhancing their overall performance.
Applications in the Pharmaceutical Industry
The pharmaceutical industry is no stranger to complex issues that require thorough analysis and resolution. The 5 Whys Root Cause Analysis technique can be a valuable tool in this sector, helping pharmaceutical companies identify the underlying causes of various challenges. From manufacturing defects to regulatory compliance issues, the 5 Whys Technique can aid in uncovering the root cause behind these problems.
Enhancing Quality Control
In the pharmaceutical industry, maintaining high-quality standards is paramount to ensure the safety and efficacy of medications. By applying the 5 Whys Technique to quality control processes, pharmaceutical companies can dig deep into the reasons behind product deviations or failures. This analysis can lead to improvements in manufacturing practices, equipment maintenance, and personnel training, ultimately enhancing overall product quality.
Streamlining Clinical Research
Clinical research plays a crucial role in the development of new medications and treatments. However, deviations in research protocols or data inconsistencies can hinder the progress of clinical trials. By utilizing the 5 Whys Technique, pharmaceutical companies can investigate the root causes of these deviations, whether they stem from procedural errors, communication breakdowns, or external factors. This analysis can help streamline clinical research processes and ensure the integrity of study results.
Investigating Deviations
Deviations in pharmaceutical manufacturing processes can have far-reaching consequences, potentially impacting product quality, regulatory compliance, and patient safety. The 5 Whys Technique can be applied to investigate deviations in manufacturing, packaging, or labeling processes, pinpointing the root cause of these issues. By addressing underlying problems, pharmaceutical companies can implement corrective actions to prevent future deviations and maintain adherence to industry regulations.
Addressing Failure Investigations
In the pharmaceutical industry, failure investigations are crucial for understanding the reasons behind product failures, equipment malfunctions, or process deviations. The 5 Whys Technique can guide pharmaceutical companies in systematically analyzing failures, delving into the series of events leading to the issue. By identifying the root cause of failures, companies can implement robust solutions to prevent recurrence, ensuring product quality and patient safety.
Conclusion: Empowering Problem-Solving in Pharmaceuticals
In conclusion, the 5 Whys Root Cause Analysis technique offers pharmaceutical companies a systematic approach to problem-solving and continuous improvement. By applying this technique to various aspects of the pharmaceutical industry, from quality control to clinical research and failure investigations, companies can uncover hidden issues, address root causes, and drive meaningful change. The 5 Whys Technique empowers pharmaceutical professionals to tackle challenges head-on, leading to enhanced quality, compliance, and efficiency in an ever-evolving industry.
Applications in Clinical Research
Clinical research plays a crucial role in advancing medical knowledge and improving patient care. The 5 Whys Root Cause Analysis can be a valuable tool in this field, helping researchers uncover the underlying causes of issues and implement effective solutions. In clinical research settings, the technique can be applied to various scenarios, such as protocol deviations, data discrepancies, and study delays. By delving deep into the root causes of these issues, researchers can enhance the quality and reliability of their studies, ultimately benefiting patients and the healthcare industry as a whole.
In Clinical Research, the 5 Whys Technique can be utilized in the following ways:
Protocol Deviations: Investigating and addressing protocol deviations is essential in maintaining the integrity of a clinical study. By employing the 5 Whys Technique, researchers can identify why deviations occurred, whether due to human error, system failures, or other factors. This analysis enables the implementation of preventive measures to reduce the likelihood of future deviations, ensuring data accuracy and study validity.
Data Discrepancies: Ensuring the accuracy and consistency of data is paramount in clinical research. When data discrepancies arise, researchers can apply the 5 Whys Technique to uncover the root cause of the discrepancies. By understanding why inconsistencies occurred, researchers can improve data collection processes, enhance data quality, and minimize errors in future studies.
Study Delays: Timely completion of clinical studies is crucial for delivering new treatments to patients efficiently. When faced with study delays, researchers can use the 5 Whys Technique to identify the reasons behind the delays. Whether it be logistical challenges, regulatory issues, or unforeseen events, this analysis can help in developing strategies to streamline study timelines and optimize research outcomes.
Quality Control: Maintaining high standards of quality control is essential in clinical research to ensure the validity and reliability of study results. By applying the 5 Whys Technique to quality control processes, researchers can pinpoint the root causes of quality issues, whether related to documentation, sample handling, or data management. This analysis facilitates the implementation of corrective actions to enhance quality assurance practices and uphold research standards.
Applications in Deviation Investigation
Deviation investigation is a crucial aspect of ensuring quality and compliance in various industries, including pharmaceuticals. The 5 Whys Technique can be a valuable tool in this process, helping organizations uncover the root causes of deviations and non-conformances. By repeatedly asking "why," investigators can dig deep into the factors leading to deviations, ultimately improving processes and preventing future occurrences. This methodical approach allows for a thorough analysis of deviations, enabling organizations to implement effective corrective and preventive actions.
In the pharmaceutical industry, deviation investigation plays a vital role in maintaining product quality and regulatory compliance. By applying the 5 Whys Technique, pharmaceutical companies can investigate deviations in manufacturing processes, equipment failures, or quality control procedures. This systematic approach helps identify the underlying causes of deviations, such as human error, equipment malfunction, or procedural issues. By addressing these root causes, organizations can enhance product quality, ensure patient safety, and uphold regulatory standards.
In clinical research, deviation investigation is essential for maintaining the integrity of study data and ensuring participant safety. The 5 Whys Technique can be used to investigate deviations in study protocols, data collection procedures, or participant recruitment processes. By uncovering the root causes of deviations, researchers can implement corrective actions to prevent future occurrences and uphold the validity of research findings. This systematic approach to deviation investigation promotes transparency, accountability, and compliance in clinical research practices.
Failure investigation is another area where the 5 Whys Technique can be applied effectively. Whether in manufacturing, service, or research settings, failures can have significant consequences on operations, product quality, and customer satisfaction. By using the 5 Whys Technique to investigate failures, organizations can identify the fundamental reasons behind the issues, such as design flaws, process errors, or environmental factors. This in-depth analysis enables organizations to implement robust solutions that address the root causes of failures, leading to improved performance and reliability.
In conclusion, the 5 Whys Technique offers a systematic and effective approach to deviation investigation in various industries. By delving deep into the root causes of deviations, failures, and non-conformances, organizations can implement targeted solutions that prevent recurrence and improve overall performance. Whether in the pharmaceutical industry, clinical research, or failure investigation, the 5 Whys Technique can help organizations uncover hidden issues, enhance quality, and drive continuous improvement. So, next time you encounter a deviation or failure, remember to ask "why" and unlock the power of root cause analysis.
Applications in Failure Investigation
Failure investigation is a critical aspect of many industries, including pharmaceuticals and clinical research. When a failure occurs, it is essential to determine the root cause to prevent future incidents. The 5 Whys Technique is a valuable tool in this process, as it helps uncover the underlying reasons behind failures, such as equipment malfunctions or process deviations. By asking "why" repeatedly, investigators can trace the failure back to its origin, enabling them to implement effective solutions and prevent similar failures in the future.
In the pharmaceutical industry, failure investigation plays a crucial role in ensuring product quality and patient safety. By applying the 5 Whys Technique, pharmaceutical companies can identify the root cause of quality deviations, manufacturing errors, or product failures. This in-depth analysis helps companies improve their processes, enhance product quality, and maintain compliance with regulatory standards. Failure investigation using the 5 Whys Technique empowers pharmaceutical companies to address issues proactively and continuously improve their operations.
Clinical research also benefits from the application of the 5 Whys Technique in failure investigation. When a clinical trial encounters unexpected outcomes or deviations from the protocol, investigators need to understand the underlying reasons to maintain the integrity of the study. The 5 Whys Technique helps unravel the complexities of clinical research failures by systematically digging deeper into the root cause. This methodical approach enables researchers to address issues promptly, mitigate risks, and uphold the validity of the study results.
Moreover, in deviation investigation, the 5 Whys Technique proves to be an invaluable tool for uncovering the reasons behind non-conformances and deviations from established processes. Whether in manufacturing, service, or research settings, deviations can impact quality, efficiency, and safety. By employing the 5 Whys Technique, organizations can pinpoint the root cause of deviations, implement corrective actions, and prevent recurrence. This proactive approach to deviation investigation helps maintain operational excellence and uphold regulatory compliance across various industries.
Conclusion
In conclusion, the 5 Whys Root Cause Analysis is a powerful tool that can help individuals and organizations get to the bottom of persistent problems. By digging deep and asking "why" multiple times, you can uncover the underlying causes of issues, rather than just treating the symptoms. While the technique has its benefits, such as simplicity and cost-effectiveness, it also has limitations, such as potential bias and oversimplification. However, when used correctly and in conjunction with other problem-solving methods, the 5 Whys Technique can be a valuable asset in various industries, from manufacturing to pharmaceuticals. So next time you're faced with a pesky problem at work, remember to peel back the layers with the 5 Whys and discover the true root cause.
Template: